
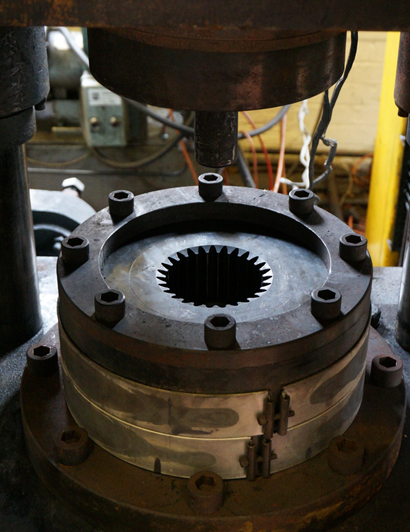
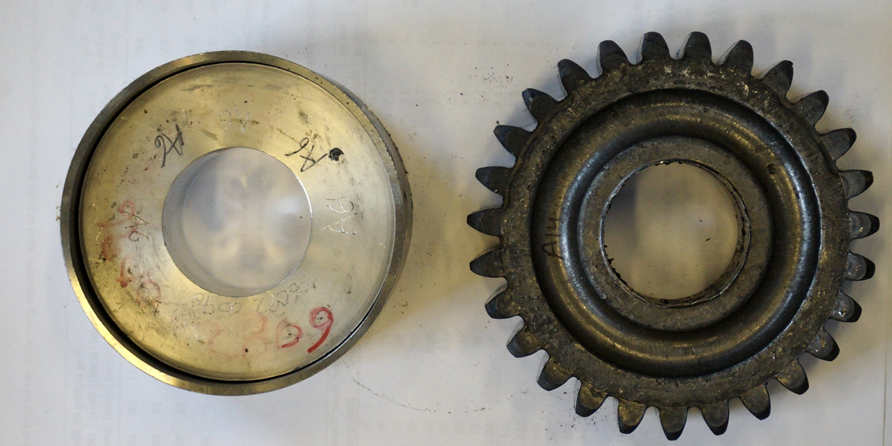

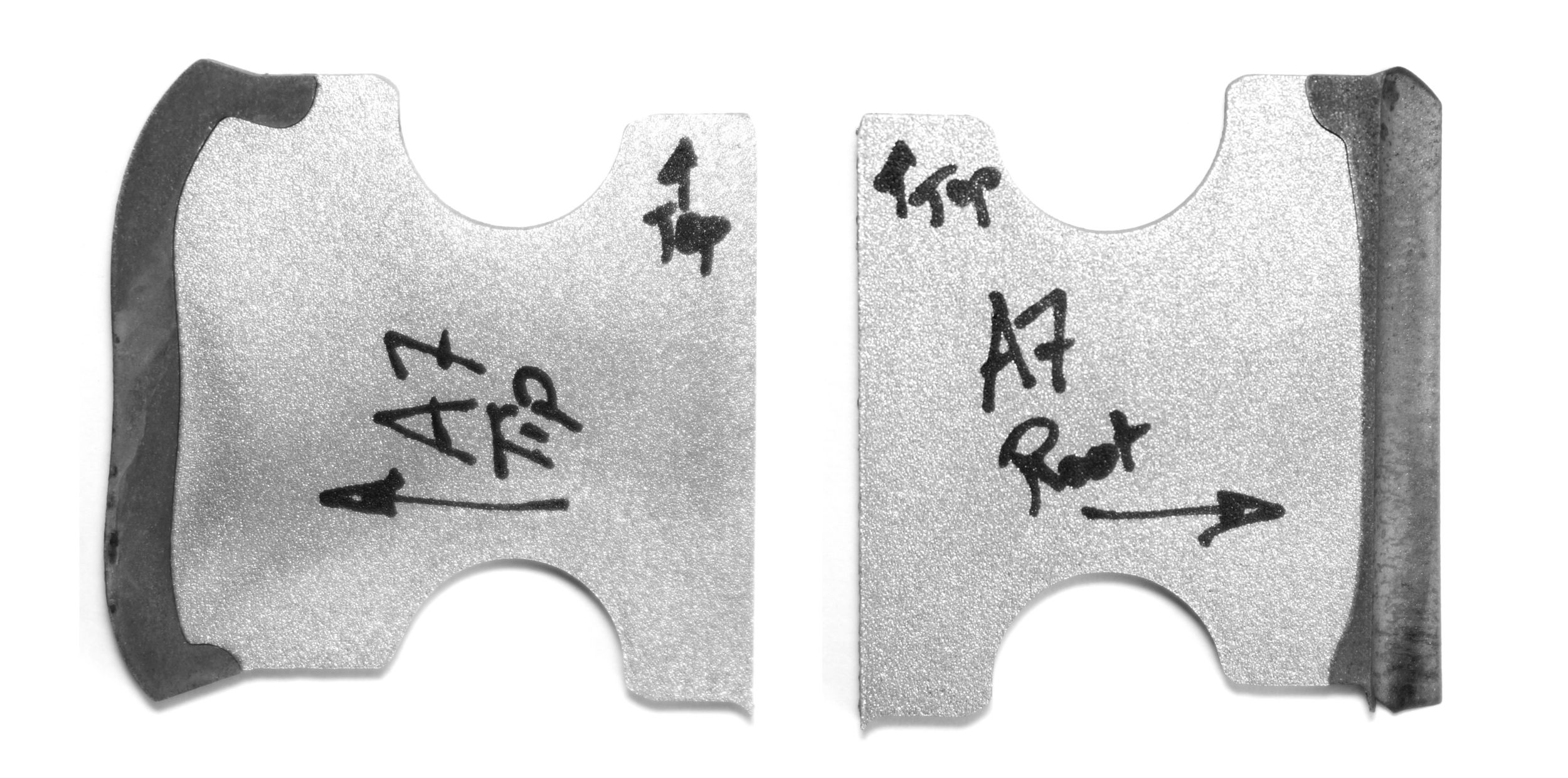
Dubai, United Arab Emirates
Tools used: Massey 1000ton forging press, general milling and turning, furnace heat treatment, EDM wire cutting, optical microscopy, scanning electron microscopy, EDX spectroscopy.
Part of an Imperial Innovations project:
http://www.imperialinnovations.co.uk/license/available-technologies/lightweight-multi-material-gears/
The objective of this process is to produce precision-forged bi-metal lightweight gears in a single step forging. Implementation of lightweight bi-metal gears to vehicle gears can result in weight savings of 30-50% over traditional steel gears.
The motivation for this is to be able to reduce the mass of rotating mechanical components, the benefit of which is substantially greater than reducing the mass of non-structural components. The vast majority of the rotational inertia of an automotive transmission comes from the gears themselves, and thus reducing this directly results in improved transient transmission performance, benefiting fuel consumption and acceleration speed.
Trials have been conducted with combinations of materials including Al-6082/Carbon Steel, and Al-7075/EN24, as well as a range of different ring thicknesses. For the experimental trials, the steel and aluminium billets were heated to their respective forming temperatures independently in two different furnaces. The workpieces were then assembled concentrically in the die, and forged in a single step operation using a Massey 1000 ton forging press.
Gears were successfully forged in the trials, and were sectioned for analysis. Preliminary evidence of a weld at the interface between the two metals in certain regions of the gears has been discovered.
Details of the experimental setup as well as detailed results re presented in my PhD thesis.
Tools used: Massey 1000ton forging press, general milling and turning, furnace heat treatment, EDM wire cutting, optical microscopy, scanning electron microscopy, EDX spectroscopy.
Part of an Imperial Innovations project:
http://www.imperialinnovations.co.uk/license/available-technologies/lightweight-multi-material-gears/
The objective of this process is to produce precision-forged bi-metal lightweight gears in a single step forging. Implementation of lightweight bi-metal gears to vehicle gears can result in weight savings of 30-50% over traditional steel gears.
The motivation for this is to be able to reduce the mass of rotating mechanical components, the benefit of which is substantially greater than reducing the mass of non-structural components. The vast majority of the rotational inertia of an automotive transmission comes from the gears themselves, and thus reducing this directly results in improved transient transmission performance, benefiting fuel consumption and acceleration speed.
Trials have been conducted with combinations of materials including Al-6082/Carbon Steel, and Al-7075/EN24, as well as a range of different ring thicknesses. For the experimental trials, the steel and aluminium billets were heated to their respective forming temperatures independently in two different furnaces. The workpieces were then assembled concentrically in the die, and forged in a single step operation using a Massey 1000 ton forging press.
Gears were successfully forged in the trials, and were sectioned for analysis. Preliminary evidence of a weld at the interface between the two metals in certain regions of the gears has been discovered.
Details of the experimental setup as well as detailed results re presented in my PhD thesis.