Reducing Forming Forces in Precision Gear Forging
Software/Equipment used: Simulia Abaqus 6.12, Instron 2.5MN servohydraulic testing machine, general milling and turning
Publication: An experimental and numerical investigation into forming force reduction in precision gear forging, 2014.
A significant factor in the cost of industrial machinery for precision forging is the maximum load required to fully forge the final shape of components. Typically in a precision forging process, the required load increases greatly towards the end of the stroke. This study focuses on reducing the final sharp increase in load encountered in a typical closed die forging setup.
In an example case of precision gear forging, it is commonly known in the literature that the final stages of filling the tooth tips with material constitutes up to 2/3 of the total press load required to forge a precision gear. This means that a significantly larger press is required to fill the tips compared to the bulk forming of the gear, thus substantially increasing the initial investment required for precision forgings compared to traditional forgings. An example of a load-stroke curve is shown in the images.
A number of tooling modifications were investigated numerically using Simulia Abaqus to produce an explicit finite-element model of the forging operation. For simplicity of the simulation and material properties, an isothermal, rate-independent simulation was developed, simulating a single tooth to minimise computational time.
This model was used to investigate a large number of tooling and workpiece designs intended to reduce the forming load. Those investigated include methods described in the literature, as well as new methods introduced in this study.
Simulations showed that the most simple and effective method involves leaving a gap at the tooth tip (the final point of filling). This method, called the “Peripheral Relief” method, allows workpiece material to flow out of the enclosed die cavity at the end of the forging operation, thus eliminating the sharp increase in forming load at the end of the forging process. An image of the FE simulation of the project is shown.
To verify the simulation, experimental trials were conducted utilising a 2.5 MN Instron dynamic testing machine. The test rig used is shown in the images, along with a resulting gear. Commercially pure aluminium was used as a model material as it is sufficiently soft for room temperature work, as well as strain rate independent, thus removing several variables from consideration.
In order to effectively utilise this method, it is necessary to carefully control the stroke of the press, to prevent excess material from being extruded from the relief port. Appropriate stroke can be determined from numerical simulations.
Force reductions of up to ~60% are possible with significant material loss at large relief port sizes, however for more practical applications, load reductions of approx. 10-30% are possible with negligible material loss.
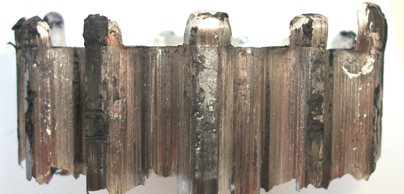