Simulation of Forged Bi-Metal Gears
Software/Equipment used: Dassault Systèmes SolidWorks, SIMULIA Abaqus 6.13, FORTRAN compiler, Imperial College HPC.
Part of an Imperial Innovations project:
http://www.imperialinnovations.co.uk/license/available-technologies/lightweight-multi-material-gears/
This project was the numerical parallel to the bi-metal lightweight gear forgings. Specifically, it is a numerical simulation of forging a steel ring and an aluminium core together to a unified bi-metal gear, reducing the mass of the part.
The objective was to generate a numerical representation of the forging process in order to determine a number of parameters, including:
(i) Overall press load-stroke characteristics
(ii) Interfacial properties, including pressure and shear
(iii) Bulk temperature to determine if any melting occurs
The numerical model was created using Simulia Abaqus 6.13. The model is of the dynamic explicit coupled temperature-displacement type. The modelling domain was chosen as half of a tooth, exploiting the inherent symmetry of the problem to reduce computational time.
Material properties are described using a material property subroutine (VUMAT) enabling accurate determination of the flow stress regardless of the temperature, strain, and strain rate at any element in the model.
Due to the large displacements and distortions occurring in the forging process, a very fine mesh is required, which is also adaptive to alleviate excess distortions. A total of 1.25 million elements were used in the workpieces, and an additional 120 thousand in the toolpieces (which we're also modelled to depict true-to-life thermal conduction).
A number of runs were conducted, adjusting the ring thickness and temperatures, to numerically analyse the actual forgings that we're conducted. Data from these simulations were used in further research into bonding at the interface.
Numerical data from the simulations are presented in my PhD thesis.
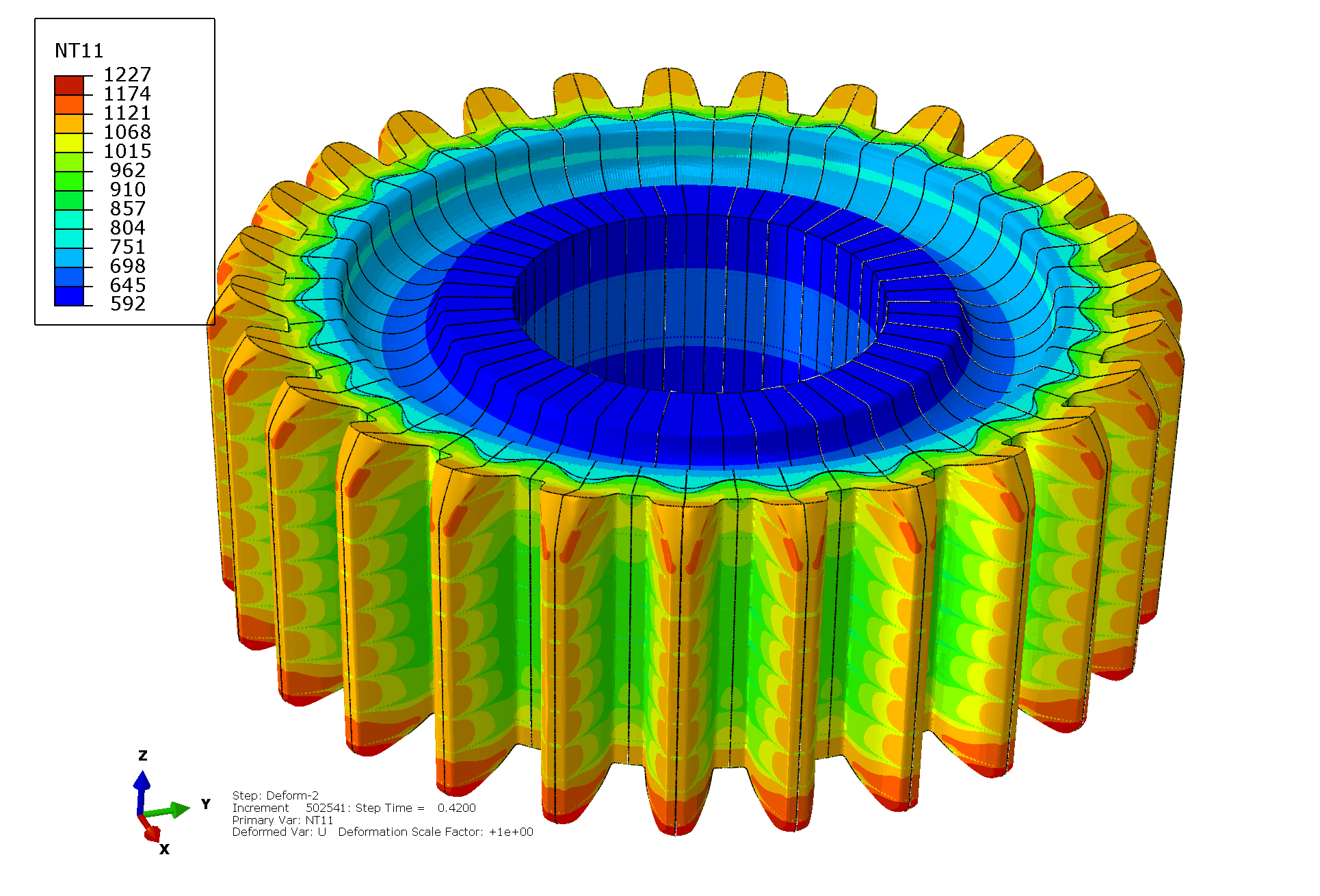
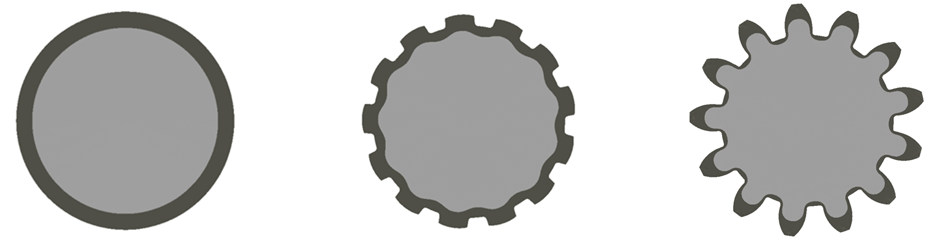
